In this article, we’ll discuss the Boston’s Big Dig Project, the causes of cost escalation during the project, the design and construction risks involved, the underground utility protection, delayed integrated project management, the benefits of partnering, and learning from the project.
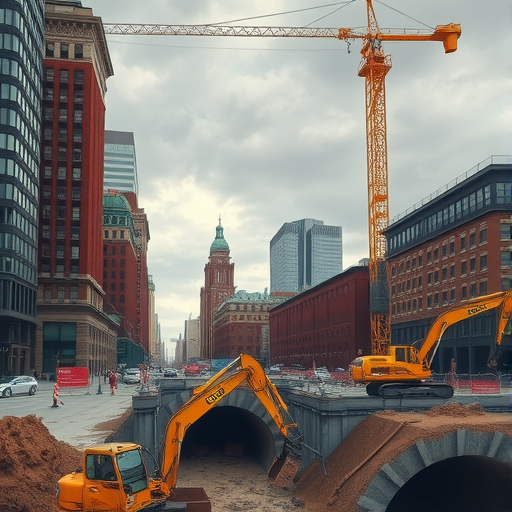
The initial cost for the Big Dig was $2.56 billion. The budget estimates went high to $7.74 billion in the year 1992, and $14.8 billion in 2007. The reasons were failing to assess conditions, inflation, mitigation and environmental costs, and scope expansion.
Feasibility and documentation were conducted before the start of the project. Costs increased throughout despite efforts to mitigate, avoid, or transfer risks and decrease costs.
Innovative insurance programs offered contractors, designers, and sub-contractors group coverage, a safety program, a cost-controlling program to save $1.2 billion, program to identify and mitigate delays, an agreement for labor for no slowdown and no strike during the project life, a program for quality assurance which was recognized by the government administration as a noteworthy initiative, and a resolution process to avoid litigation costs.
Causes of Cost Escalation in the Boston’s Big Dig Project
Research on the project indicates a cost escalation. Multiple project management decisions added to it. The main reason was a lack of knowledge and experience to deal with the uncertainty and complexity.
Inflation was the main reason for cost escalation. Some of the cost increases can be related to estimates.
Design and Construction Risks in the Boston’s Big Dig Project
Risks included archeological discoveries, unchartered utilities, ground conditions, weak soil, and environmental issues. The project faced milestones and schedules, and design issues. The discovery of an old-era site and artifacts was a surprise that added to the complication and delays, requiring stakeholders’ approvals.
Underground Utility Protection in the Boston’s Big Dig Project
To address the losses from the failure of utilities underground, a utility program relocated about 19 miles of electric, sewer, gas, water, telephone, and other lines maintained by 31 companies in the year 1996. Some of the infrastructure was 150 years old. The project needed to deal with utilities shown on drawings that were never installed, and flooding and damage due to underground pipes of sewer not present on the drawings. With big buildings within a few feet of the construction, there was a high risk of damage to infrastructure and a shutdown of operations of one of the major Boston financial centers. A single wrong move could have led to the closing of the Federal Reserve Building and affected the financial system of the country for years.
The project required about 5,000 workers to work all the time and 80,000 construction hours. From 1996 to 2000, the utility damage rate decreased by 86 percent, with a $50 million cost savings. Despite the risks, the program improved quality, budget, and public relations.
Delayed Integrated Project Management in the Boston’s Big Dig Project
The project relied on an integrated team that included all of them to make decisions.
Integration problems started from the external and internal project stakeholders, their changing relationships, and interactions. The project suffered from complex processes that led to difficulty in enforcing uniformity.
In the initiation phase of the project, there was too little communication between many external and internal project stakeholders, other than the community outreach, specifically the residents who lived close to the project sites. Social and community costs were underestimated during the project. The government served the role of owner and regulator. An integrated project should have centralized accountability and decision-making for all basic project functions.
The Benefits of Partnering
Partnering is these days used widely by many construction and government entities around the globe. It involves sharing risks from the project and promoting and establishing relationships. Partnering involves problem-solving between contractor and owner. In the Big Dig project, partnerships improved adherence to safety and performance of the project, reduced claims, costs, and litigation.
Partnering was implemented in the project in 1992, but as it succeeded, it was also started to use elsewhere. Although partnering is not always a requirement, on this project it was part of all construction contracts.
Sessions were conducted regularly to discuss needs, improve controls, and resolve issues. Partnering activities involved seminars, training, and meetings. State and Federal government contractors and officials met regularly with experts to assist in developing an integrated single team.
One example is the Big Dig leaks which caused a delay in construction and had several flow paths and causes. Government lawyers spent about two thousand hours trying to assess the responsibility. The leak was due to issues with contractor performance and site conditions. To avoid high-cost litigation, the Metropolitan Authority decided to mediate before judges.
Risks must be shared between partners when possible to encourage continuous improvement and innovation, particularly where risks are known and technology is new. On the project, risks were shared between the contractors and the owners for technology interfaces among contractors, and deep connections underwater.
Teaching the skills to solve problems is a main benefit. Never use partnering instead of rigorous and independent oversight.
Learning from the Project
Mega projects face difficulties due to unforeseen events, technical complexities, regulatory requirements, political environment, and community concerns. From the Big Dig project, we have learned the following lessons:
Project integration is the key to success.
Incentives must be part of contracts throughout the project lifecycle for quality, financial soundness, schedule, and budget.
Oversight and continuous improvement are both crucial. Working the way work has always been done does not apply to mega projects that need a culture of collaboration and constant innovation.
Learning from the Boston’s Big Dig Project- FAQs
How did the Big Dig affect the environment?
The project affected the air and the land. The project required moving large amounts of dirt and sediment to start the construction. This could destroy the habitat of small mammals and birds.
What was the purpose of the Big Dig in Boston?
The project improved mobility and reduced traffic in a congested city.
Is Boston’s Big Dig considered a success?
The project resulted in a 62% reduction in travel hours on the I-93, the Storrow Dive, and the airport tunnels from 38,200 hours to 14,800 hours per day.
What were the problems with the Big Dig?
The biggest problem with the project was the poor quality of the soil. Placing the boxes of the tunnel without stabilizing the soil could lead to the settlement of the railroad tracks and threaten train service.
Do follow our Case Studies Section for more relevant articles
Do watch the Article Video Here
Do subscribe Our YouTube Channel Here